How coffee shops can improve their cold brew
Perfect Dailey Grind • March 2024
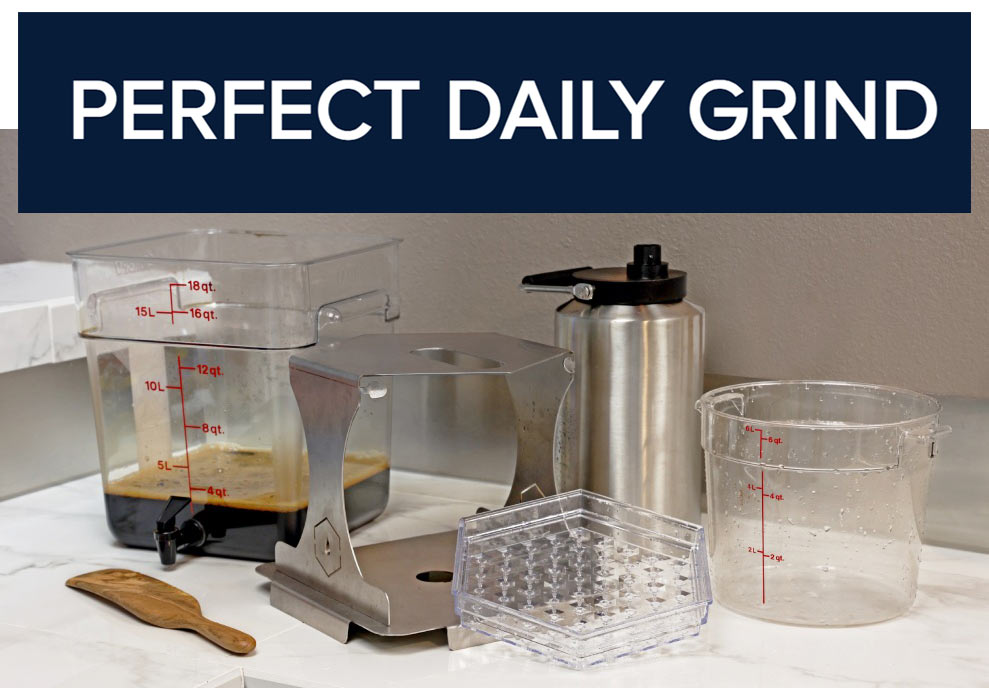
According to the National Coffee Association’s (NCA) fall 2023 National Coffee Data Trends report, consumption of cold brew in the US alone has increased by a staggering 300% over the past seven years. And the world over, this trend shows no signs of slowing down anytime soon.
Despite being available on most coffee shop menus today, cold brew doesn’t always receive the same level of attention to detail as other beverages. However, as its popularity continues to soar, café owners and baristas are looking for new ways to stand out in an increasingly competitive cold coffee market.
A big part of this is capitalising on the rapid innovation in cold brew technology. Now more than ever, there are a number of machines available which can prepare cold brew in much shorter time frames – helping coffee businesses cut costs, improve efficiency, and scale their offerings more sustainably.
Read MoreTorr Launches the Hive Cafe Countertop Coffee Concentrate System
Daily Coffee News | Roast Magazine • Jan 2024
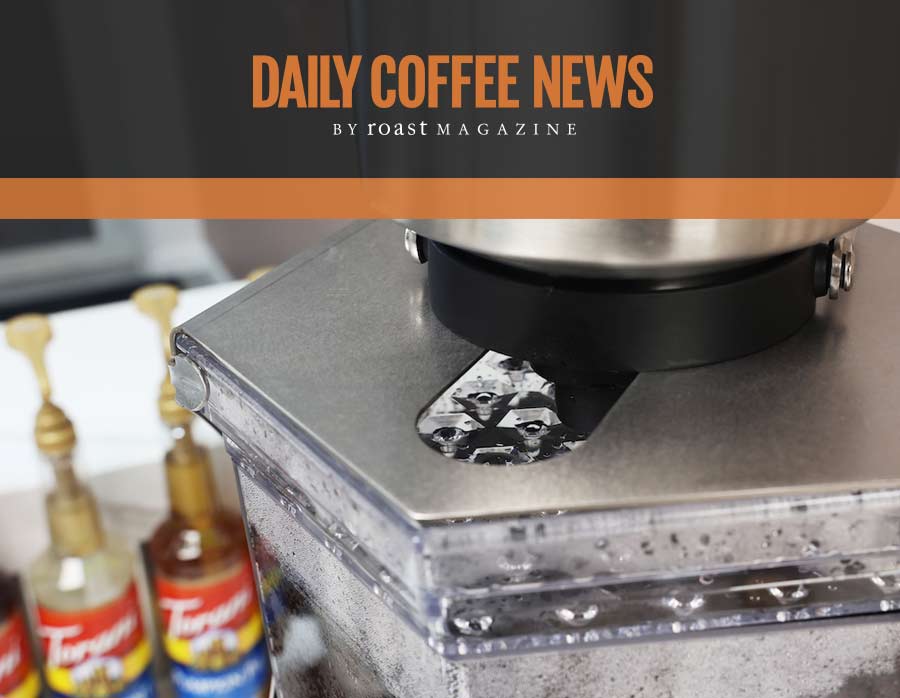
Commercial cold coffee equipment company Torr Industries recently rolled out a countertop-friendly version of its signature Hive Brew cold coffee system, called the Hive Cafe.
The northern California coffee company has also broadened the capabilities of the Hive platform to include batch brewing of espresso-like concentrate, alongside existing cold brew coffee brewing.
The Hive Cafe is a simplified semi-automatic system intended for use by individual coffee shops or small chains with modest demand for fresh daily coffee concentrate.
Baristas pre-wet up to 1 kilogram (2.2 pounds) of dry ground coffee prior to loading the patented Hive brewing chamber. Above that, the barista positions a 1-gallon steel fresh water container.
Read MoreFlexible Packaging for Wine
Wine Business Monthly Magazine • December 2022
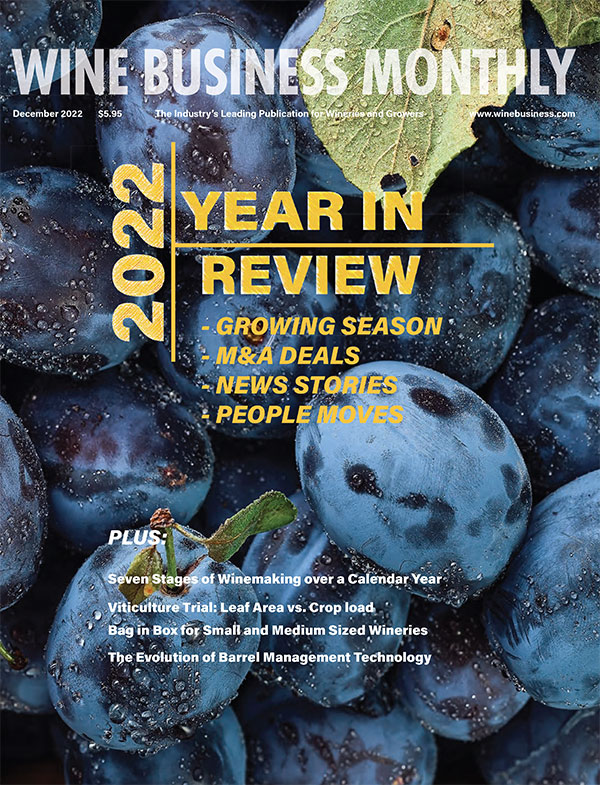
Bag in Box (BIB) wine packaging has become a staple in the wine industry. In the past 10 years, there have been improvements in this technology that warrant a review and also an assessment of the climatological impact of BIB wine products as compared to glass bottle packaging. Here we offer two companies as examples of the BIB production sector: one for equipment and one for packaging materials. A list of the flexible packaging companies on the WinesVinesAnalytics.com website is included in Box 1.
Wine consumers, as well as many people in the wine industry, think that BIB packaging was only for large-scale wineries that operate on low margins, have large volumes and sell value-priced wines. New systems with improved technology now allow all sizes of wineries, including those with smaller production capabilities, to enter this market. With the right business decisions, it can be both profitable and environmentally-sound for wineries to use BIB packaging and significantly reduce their carbon footprint.
With the interest in global warming and its causes, there is demand for the wine industry to lower its carbon footprint and transition into more sustainable operations. Indeed, several distressing but important pieces of information emerge that the wine industry should begin to address now to prepare for a more sustainable future...
"TORR Industries has also been at the forefront of design changes to meet the ergonomic aspects of packaging"
Read MoreTorr Industries Buzzing with New Hive Brew Scalable Cold Brew System
Daily Coffee News by Roast Magazine | Howard Bryman • August 2022
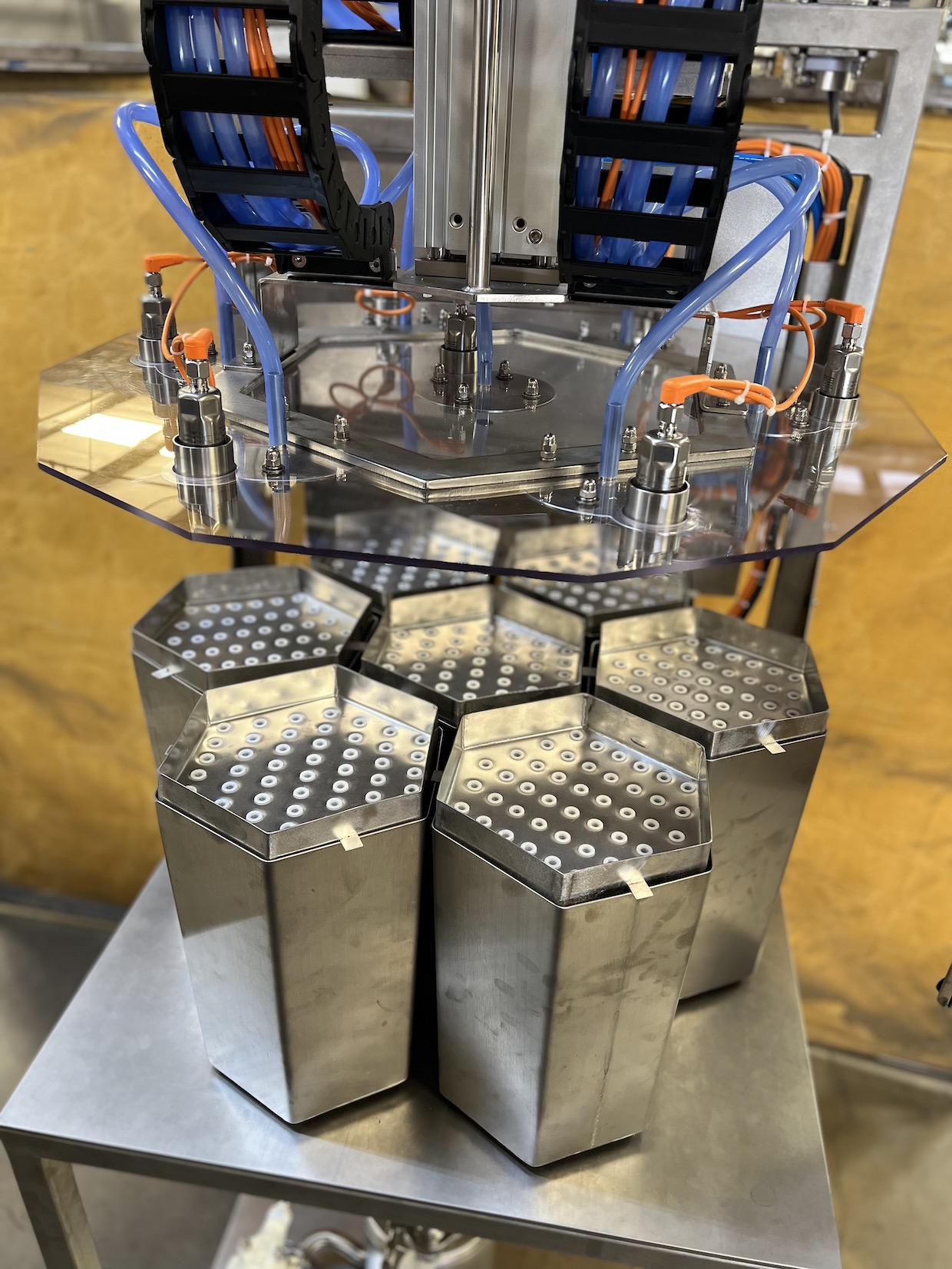
The Hive Brew 700 industrial cold brewing machine. All images courtesy of Torr Industries.
Redding, California-based production equipment manufacturer Torr Industries is giving new shape to cold coffee production, and it’s hexagonal.
Torr’s new cold coffee production system called Hive Brew builds upon the brewing technology the company introduced last year with its Brew50, Twinbrew and Quadbrew cold coffee brewing systems.
Maintaining those systems’ controlled percolation technique, the Hive Brew system veers from the individual brew chamber design and instead performs extractions at scalable volumes through a modular array of small, equally sized hexagonal brew cells.
The Hive Brew 100 is a manually operated single-cell version that replaces the Brew50. Its lone hexagonal brew cell holds anywhere from 1-6 pounds of pre-wetted ground coffee, and yields as much as 8-10 gallons of RTD brew at 2.0 Brix within about 25-30 minutes.
The Hive Brew 700 module contains seven hexagonal brew cells that are positioned closely together in a honeycomb formation. The machine performs seven small-batch extractions within each cell simultaneously. The result is a cumulative 70 gallons of RTD cold brew coffee per 30-minute batch.
Through an Allen-Bradley PLC control system, users can set one profile for all seven cells for a single larger batch, or customize the water temperature and flow rate for seven completely different batches.
“There are different methods of doing cold brew; there’s not one cold brew,” Randy Anderson, an independent cold brew consultant who helped Torr Industries develop its systems, told Daily Coffee News. “If you can control the speed of the water going through the grounds, and you do it at a temperature that minimizes the effects of titratable acidity that you find when you’re doing hot coffee, and you can minimize the changes between chlorogenic acid and the development of quinic acid, you have a successful cold brew. You can still have a lot of flavor; you can have a very smooth drink; and you can have an efficiency or an extraction percentage that is in the 20s, not in the teens.”
To scale up from a Hive Brew 700, as many as eight Hive Brew 700 modules can be daisy-chained together for control by a single PLC unit. The maximum 56-cell system is capable of producing roughly 5,000 gallons of RTD cold brew within an 8-hour shift while maintaining micro-batch precision and extraction efficiency within each cell, and avoiding many of the challenges common to high-volume cold brew production, according to Torr Industries Founder Tim Orr.
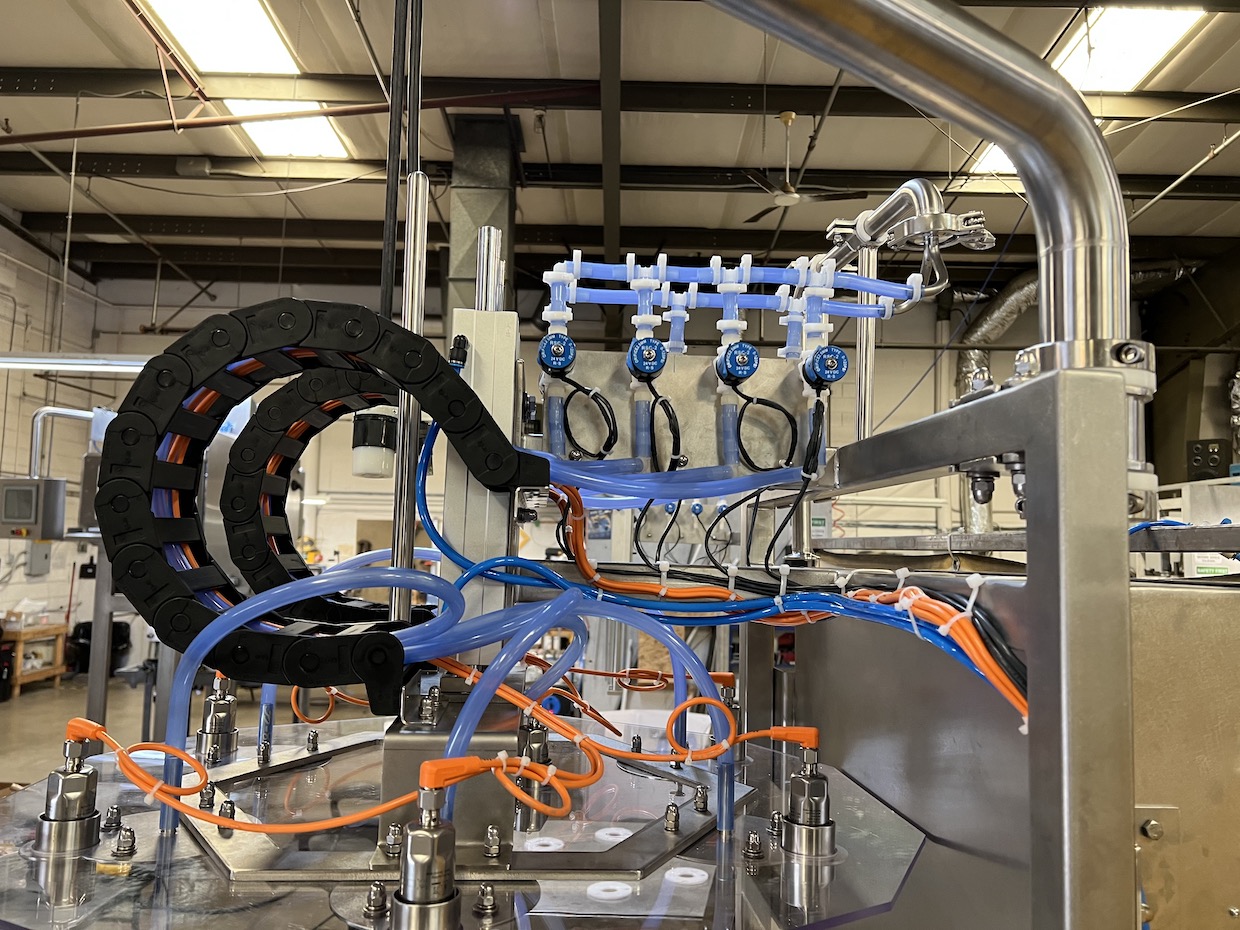
“It was like one of those a-ha moments,” Orr told Daily Coffee News. “If you do a small five or six pound brew, you always get a really good extraction percentage and you never lose a batch from what I call a ‘CO2 balloon’ [that] creates an inversion layer inside the bed, [causing] the water to shed off of it like an umbrella. So then I thought, ‘wow, all we have to do is nest these in a hive.’ Now we can brew a lot of coffee, but we always have a controlled brew.”
Each Hive cell has a screen at the bottom that mainly serves to break the surface tension of the descending liquid to alleviate channeling, but also serves as an initial filter. Two more easily rinsed steel plates beneath the screen catch any sediment that may pass through. The machine also calls for pre-wetting grounds before manually loading the mixture into the cells.
Said Orr, “The real filter in our technology is the coffee itself, because it’s [pre-wetted], and the water runs through it slowly enough that the coffee grounds itself holds the fines in the bed itself.”
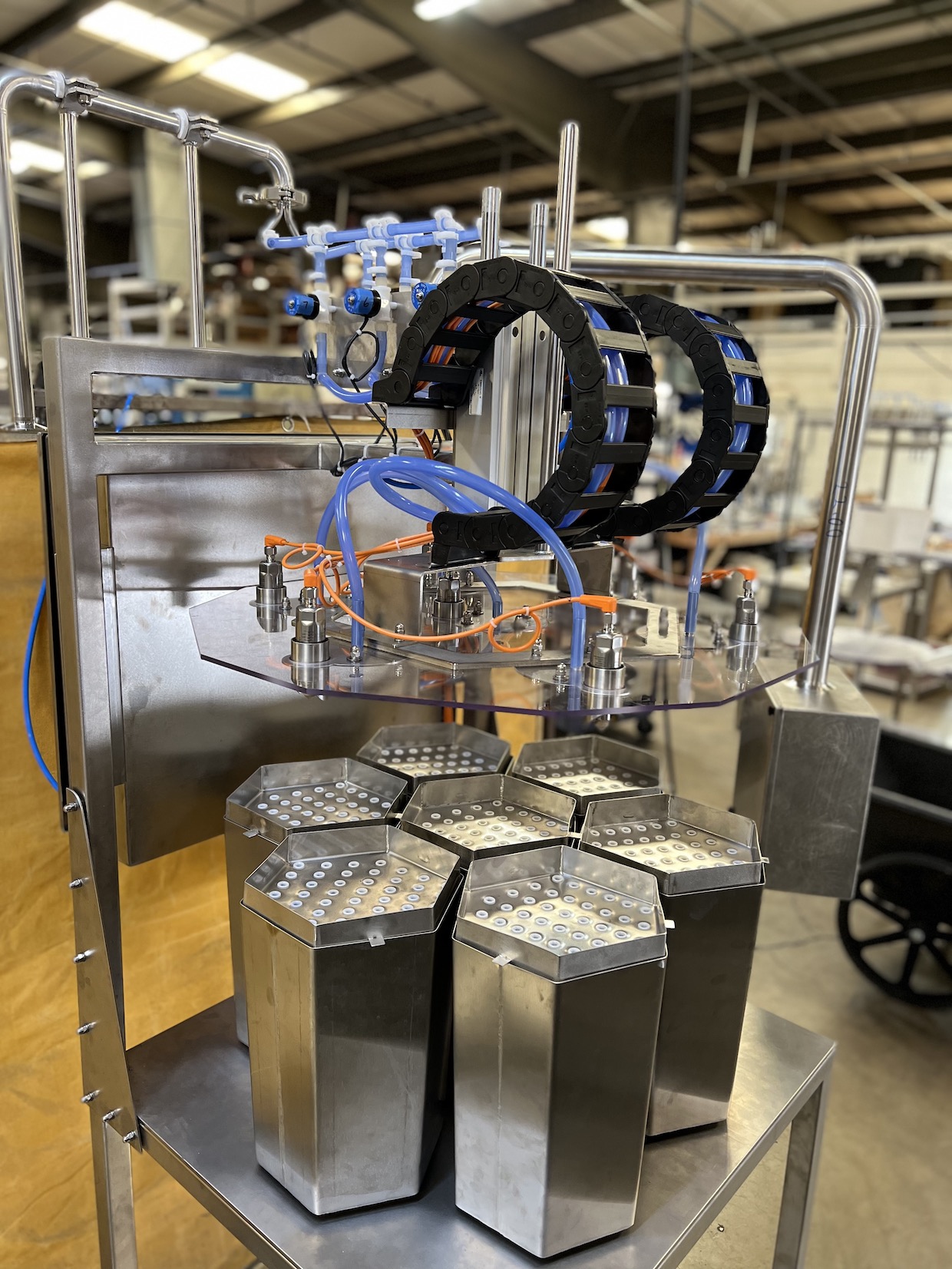
Orr said the company plans to roll out an additional piece of equipment this summer that handles the pre-wetting and loading of coffee automatically.
Legacy Brew50, Twinbrew and Quadbrew systems will continue to be supported while Torr shifts production and development entirely to its Hive Brew system, which can also be used for tea, cascara and other beverages. The company also offers custom design solutions for companies looking to scale brewing to even larger volumes.
Single-cell Hive Brew 100 units are currently priced at $8,000, while the 7-cell Hive Brew 700 system starts at $59,500, depending on supply chain conditions.
TORR Packaging Bag-in-Box Wine Packager
Wine Business Monthly Magazine • April 2022
Scholle first developed bag-in-box packaging for battery acid in 1955 and just 10 years later Th omas Angove first put wine in a flexible bag. Today, the bag-in-box wine business has grown to become a major player in wine packaging. Putting wine in a plastic bag may seem like a simple process, but in reality it is a major technical challenge to do and to do well.
All commercial wineries using bag-in-box packaging must address the issues of oxygen pickup during packaging, accuracy of the fill, sanitation of the fill, smoothness of operation so as not to damage the product, and speed of the process to keep cost of production low. All these tasks are diffi cult to accomplish with a packaging system that is so fragile that a tiny sharp point in the wrong place can ruin a whole pallet of wine if a bag on top leaks onto the boxes below.
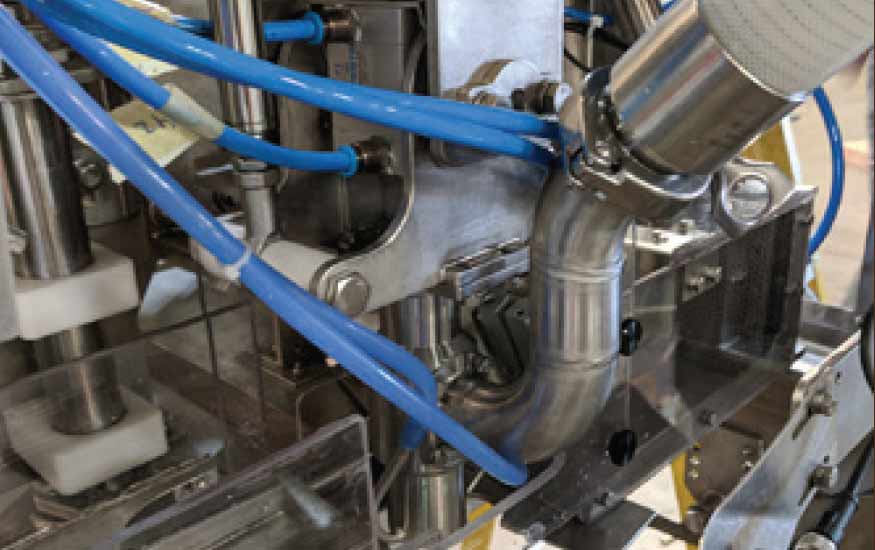
Why it’s Cool: TORR Industries has introduced several new components on their bag-in-box filling systems that answer the above issues that have been persistent irritants in the flexible packaging industry. The company has designed a new fill head that can reduce oxygen pickup to limit the pickup to about 2 ppm total oxygen in the bag after packaging. They have updated their packaging system so bags are automatically inserted into a box that is erected seconds before the bag is fi lled and immediately sealed. Th e line isfully automated, with the operator keeping the bags moved into place for fi lling and then removed offline onto pallets at a rate of up to 20 3L bags per minute.
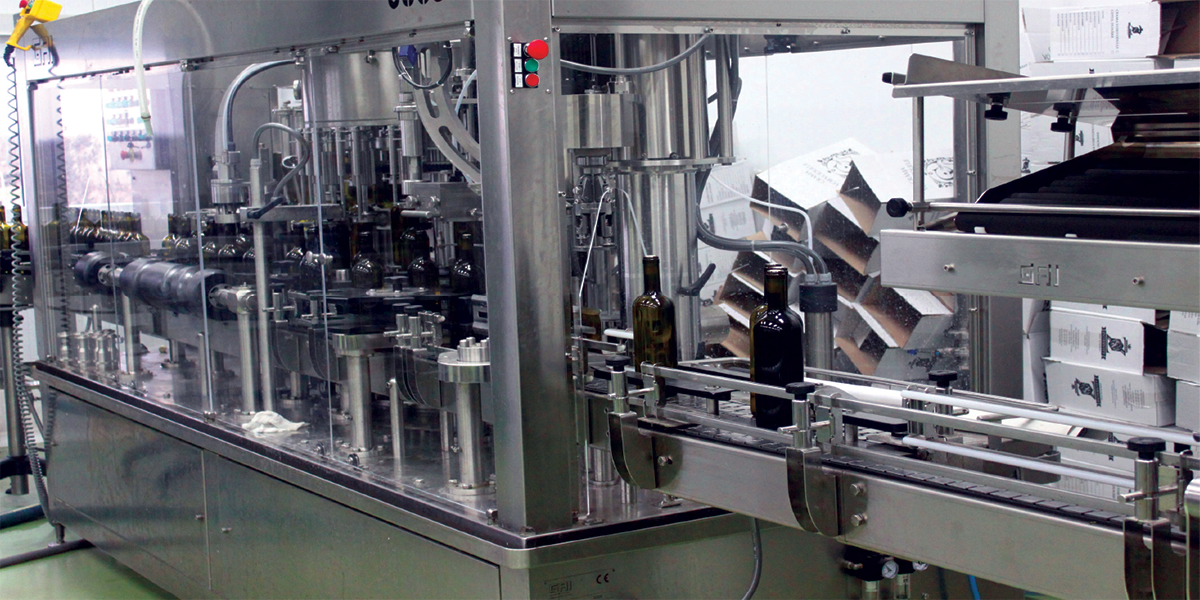
Modern Approaches to Alternative Wine Packaging
By: Alyssa L. Ochs • The Grapevine • November - December 2020Long gone are the days when wine only came in standard bottles. For some traditionalists, this is a tragedy, but for many wine enthusiasts, it’s an exciting time for innovation in the industry.
Modern technology has paved the way for wine to now be packaged in cans, boxes, bags and pouches. There are pros and cons to each packaging method, yet single-serve portability is a top priority among wine consumers, driving growth in the alternative packaging industry.
Types of Alternative Wine Packaging
One of the main bottle alternatives on the market today is wine in cans. Aluminum cans are a popular option because they are recyclable, easy for on-the-go consumption and offer a single-serving option for enjoying wine. Wine boxes, also known as bag-in-the-box, feature an air-tight bladder inside a paperboard container. This type of packaging is cost-efficient for the manufacturer and the consumer, and it’s easy to pour and reuse for multiple wine-drinking sessions.Tetra paks are mostly made from recyclable materials, making them an eco-friendly wine choice with air-tight seals for long-lasting wine. Another option is lighter-weight glass bottles, which reduce the thickness of the glass wall and remove the indentation from the bottom of the bottle. Flat wine bottles were first introduced as novelty gifts, but they are also viable alternatives for taking up less space, reducing transportation costs and reducing a wine producer’s carbon emissions.
Meanwhile, kegged wine has been growing in popularity as an on-premises option and offers by-the-glass pours at restaurants and bars. The next wave of wine products is getting even more creative with wine packaged in tubes, triangular- shaped bottles and other eye-catching specialty shapes that capture the imagination.
Pros & Cons of Packaging Options
As with all aspects of winemaking, there are pros and cons to the various wine packaging options available to wineries today. Many alternatives weigh less, don’t break as easily and produce fewer greenhouse gases than traditional bottles. Alternative packaging allows for more experimentation opportunities for wineries curious to try creative flavor profiles in single-serve portions.
Tim Orr, the president of TORR Industries in Redding, California, told The Grapevine Magazine that some alternative packages are beneficial because they offer more advertising space than glass bottles, which only have a few inches of space for branding. Founded in 2007, the TORR Industries management team has over 50 years of combined experience in filling bag-in-box, stand-up pouches and shelf-stable extended shelf-life food products, as well as bulk aseptic packaging. TORR designs and manufactures wine filling, packaging and dispensing solutions in its Northern California facility.
Alternative packaging options typically succeed better than bottles at allowing the same container of wine to be enjoyed over multiple days. However, wine may not age as well in alternative containers, which is a problem for certain types of wine. Glass bottles excel at keeping oxygen and microbes out of the wine and preventing it from going stale or growing mold while retaining the best flavor. Although attitudes are changing, the perception still exists that wine in alternative packaging is of lower quality than wine in glass bottles.
Cost Considerations
Although style is important when choosing wine packaging, the ultimate decision often comes down to cost. Bag-in-box wine is economical, and by putting more premium wine into boxes, a producer’s profit margin may increase. Transportation costs can be lower for alternative packaging because lighter loads without heavy glass are cheaper to carry, especially when shipping wine across the country or overseas.However, packaging costs may increase if a winery chooses to switch gears entirely and buy expensive equipment to accommodate new packaging strategies. This is especially true if a winery is still in the experimental phase of package design and isn’t yet sure if the packaging style will resonate with consumers or maximize product quality over time.
Life Expectancy Considerations
The amount of time that wine stays fresh should always be a top priority when choosing a packaging strategy. Glass bottles are known for their long shelf life and can last for decades because glass does not chemically react with the wine.Wine packaged in cans should have adequate acidity to maintain the freshness of flavors and help it last longer. There have been considerable strides in technological improvements for both oxygen control and bag films. Ten years ago, consumers would often find bag-in-box wine to have inconsistent taste and quality. However, this is hardly a concern today, thanks to the high-tech fillers propelling this industry into the future.
Machinery for Different Packaging Strategies
When a winery decides to change packaging types, it often needs to upgrade its equipment to handle new demands or outsource packaging to a specialized company. The machinery required to make a switch may include canning machines and filling equipment.Delkor Systems has recently developed cutting- edge packaging machinery for the wine industry – Delkor’s Performance Case Packer with patented Intelligent Synchronization technology. Based in St. Paul, Minnesota, Delkor makes case packers for bottled, pouched, canned and bag-in-box wine, as well as cartoning machines for canned wine and a bag-in-box closing machine. The Intelligent Synchronization equipment design is compact and new to the wine industry, offering two useful applications: the automatic cartoning of eight-ounce wine cans into four- and six-count paperboard cartons, and case packing of the paperboard cartons into boxes for shipment.
“It controls product flow and pattern building, effectively reducing machine footprint, costs and changeover time,” Dale Andersen, the president and CEO of Delkor, told The Grapevine Magazine. “With Intelligent Synchronization, Delkor has been able to reduce the footprint of its wine can carton loader or wine can carton case packer to just a sixby- six-foot frame and reduce machine changeover to less than eight minutes.”
Andersen said that this technology would eventually replace current case packer designs because it does electronically what many machines currently to do mechanically. This “smart machine” eliminates guide work and other machine points that cause both container and label damage, so it is natural for use in the wine industry. In 2021, Delkor will be introducing a compact Performance Case Packer for wine bottles and one for bottle unloading – both with its patented Intelligent Synchronization.
Following What’s In-demand
While weighing the options of packaging types to use for wine, learn about what’s most in-demand with consumers right now and why. Currently, top priorities among wine drinkers, especially the younger generation, are portability, on-the-go usage and discretion. Alternative containers can also offer the benefits of being less breakable and having a different type of wine for your second glass instead of committing to an entire bottle of the same wine.Bag-in-box wine has become increasingly popular during the COVID-19 pandemic because of budget concerns and more time spent at home rather than going out to wineries and bars. Even before this, bag-in-box wine gained significant traction among younger drinkers between the ages of 21 and 35. Another consumer demand is a heightened focus on environmental sustainability, which can be addressed through packaging design.
Wine Packaging Trends
It may be essential to observe wine trends when reconsidering how to package wine. Right now, there is a movement to make wine more affordable and accessible to new consumers – often younger consumers who have different standards and preferences than wine drinkers who have been enjoying bottles for decades.There is also a trend of putting higher quality wine into alternative forms of packaging, hoping to change the perception of non-bottled wine and open up people’s minds about what makes a good wine. These higher-quality offerings, paired with more creative marketing and advertising strategies, catch new consumers’ attention. That attention then propels alternative packaging products forward and opens up the market for new packaging players with innovative ideas.
Orr of TORR Industries has noticed a huge growth in the bag-in-box wine industry and much more demand since the start of the COVID-19 pandemic. He said that canned wine has seen a growth curve of around 1%, where bag-in-box packaging is closer to 20% of wine sales, up from approximately 15% a couple of years ago.
“I attribute this to the fact that the stigma of boxed wine is going away since this is a great option for not having to drink the whole bottle because coronavirus is leading to more home consumption and because of better techniques to control the oxygen.”
Orr said that his company is building and selling equipment to top wineries because it injects nitrogen and vacuums the bag to purge the oxygen before filling. In this way, his machinery gets oxygen levels down under 2% rather than the 20% standard that this packaging used to have with older technology.
Andersen of Delkor has observed that the movement of wine into cans is a significant change in the industry. He and Ryan Broughton, Delkor’s sales manager, told The Grapevine Magazine that what their customers in the beverage industry are talking about most is single-serve. Cans offer an alternative for a new class of wine consumers not focused on the quality aspects of glass bottles, but more on convenience. According to Andersen, “one could make the argument that this is a totally new market opportunity, so it is making the circle bigger rather than taking market share away from current wine sales.”
Choosing the Right Packaging
Each type of wine packaging has its benefits, so the choice largely comes down to the winery’s goals, budget and target consumer. However, different styles of wines do better in various types of packaging. For example, some wineries keep sparkling wine and aged red wines in bottles but put experimental and mid-range wines into alternative packaging to test it with their customer base.To choose the right packaging for your wine, assess current customers as well as those you want to attract in the future. Consider how much and how often you ship wine to determine if alternative packaging can help save on shipping and transportation. Determine per-unit costs and ensure that new production costs will fit within your budget. Also, think about how a change in wine packaging may impact the perception of the winery’s brand. If using multiple types of packaging, it may be a good idea to keep a few things consistent – such as the logo or colors – across all forms, to keep your brand recognizable.
Orr of TORR Industries would advise a winery looking to try alternative packaging to “understand the market, look at the viability of bag-in-box, and look at the growth curve.” His other piece of advice is to find a winery that does co-packing and set up a small contract packing arrangement to test out alternative packaging for your winery.
For wineries looking to try packaging alternatives to glass for the first time, Broughton of Delkor suggested “looking for a system that has good capability, that can adapt to ever-changing needs and that can produce small pack and large pack counts.” Delkor’s Andersen suggested having a machine that can handle both traditional bottles and cans for single-serve. “Have a plan to address single-serve because demand is increasing, and your machinery must be able to keep up with this.”